Stand Out in the Job Market with GMP Certification
Hygiene is a cornerstone of GMP, ensuring products are manufactured in a clean, contamination-free environment. This includes maintaining sterile facilities, enforcing strict personal hygiene for employees, and implementing cleaning protocols for equipment and surfaces.
I. Introduction
A. Definition of GMP (Good Manufacturing Practices)
GMP refers to a set of regulations ensuring the consistent production of high-quality products across industries like pharmaceuticals, food, and cosmetics. These practices cover aspects such as facility cleanliness, equipment maintenance, and employee training. By following GMP guidelines, businesses ensure their products meet safety, quality, and efficacy standards. Originating from international organizations like WHO and FDA, GMP forms the backbone of manufacturing compliance, creating trust among consumers and aligning products with regulatory expectations.
B. Importance of GMP in Ensuring Quality and Safety
GMP is critical for ensuring that manufactured products consistently meet defined safety and quality standards. By implementing rigorous hygiene, process control, and documentation practices, GMP minimizes risks such as contamination, mix-ups, and defects. These measures are crucial, especially in industries like pharmaceuticals and food, where quality lapses can impact public health. GMP's role extends beyond compliance, building consumer trust and protecting businesses from legal and reputational damage.
II. Core Principles of GMP
A. Hygiene and Cleanliness Standards
Hygiene is a cornerstone of GMP, ensuring products are manufactured in a clean, contamination-free environment. This includes maintaining sterile facilities, enforcing strict personal hygiene for employees, and implementing cleaning protocols for equipment and surfaces. Regular inspections and monitoring prevent microbial growth and cross-contamination. Adherence to these standards is vital in industries like food and pharmaceuticals, where lapses in hygiene can lead to serious health risks and regulatory penalties.
B. Documentation and Record-Keeping
Documentation ensures traceability and accountability in manufacturing processes. GMP mandates detailed records of production, quality checks, and deviations to ensure consistency and compliance. These documents serve as proof during audits and help identify issues during investigations. Proper record-keeping also supports continuous improvement by analyzing past performance. Inadequate documentation can lead to regulatory action, highlighting its importance in maintaining transparency and operational integrity.
C. Process Validation and Quality Control
Process validation ensures that manufacturing processes consistently produce high-quality products. GMP requires testing and monitoring each stage, from raw materials to finished goods. Quality control involves verifying product specifications through inspections and laboratory testing. These practices ensure consistency, safety, and compliance with regulatory requirements. By addressing potential risks proactively, process validation and quality control contribute to robust manufacturing systems and customer satisfaction.
III. Benefits of GMP Certification
A. Enhanced Product Quality and Safety
GMP certification ensures that products meet rigorous quality and safety standards, protecting consumers from harm. By adhering to structured processes, companies minimize risks like contamination and defects. Improved quality translates to fewer recalls, reduced waste, and higher customer satisfaction. This focus on safety and reliability is especially critical in industries like healthcare and food, where lapses can have severe consequences.
B. Increased Consumer Trust and Satisfaction
GMP certification fosters trust by guaranteeing that products are consistently safe and of high quality. Consumers feel confident choosing products from certified manufacturers, knowing they meet global standards. This trust enhances brand reputation and drives customer loyalty. Additionally, the emphasis on compliance reassures stakeholders, building long-term relationships and ensuring market competitiveness.
C. Improved Operational Efficiency and Compliance
GMP-certified organizations benefit from streamlined processes, reducing inefficiencies and errors. Clear guidelines for production, documentation, and training enhance operational discipline. Compliance with GMP also reduces the risk of regulatory penalties, costly recalls, and product rejections. By maintaining consistent quality, businesses achieve better resource utilization, ultimately lowering costs and increasing profitability.
IV. Steps to Achieve GMP Certification
A. Conducting a Gap Analysis
The first step toward GMP certification is a thorough gap analysis, identifying areas where existing processes fall short of GMP requirements. This assessment helps prioritize corrective actions and allocate resources effectively. By involving all departments, organizations can uncover hidden issues and create a roadmap for improvement. A well-executed gap analysis lays the foundation for successful GMP implementation, saving time and costs during the certification process.
B. Implementing GMP Guidelines and Protocols
Once gaps are identified, organizations must implement GMP protocols tailored to their operations. This involves establishing hygiene practices, creating documentation systems, and training staff on compliance. Changes may also include facility upgrades and process redesigns to meet GMP standards. Proper implementation ensures readiness for audits and builds a culture of quality within the organization.
C. Preparing for the Certification Audit
Preparation for the GMP audit includes a thorough review of implemented protocols, staff training, and documentation. Mock audits help identify potential non-conformities, ensuring readiness for the final assessment. Effective communication with auditors and prompt resolution of issues during the audit are crucial. Successful certification demonstrates the organization's commitment to quality and compliance, opening doors to new market opportunities.
V. Key Requirements for GMP Compliance
A. Facility Design and Maintenance
GMP compliance begins with well-designed facilities that prevent contamination and ensure smooth workflow. Proper ventilation, lighting, and drainage systems are essential for maintaining hygiene. Facilities should be regularly cleaned and maintained to avoid equipment malfunctions and ensure safety. Dedicated zones for storage, processing, and packaging minimize cross-contamination risks. By adhering to these design principles, companies create an environment conducive to producing high-quality, compliant products.
B. Staff Training and Competency
Trained personnel are crucial for effective GMP implementation. Employees must understand the importance of hygiene, proper handling techniques, and documentation practices. Regular training programs ensure staff stays updated on evolving GMP standards and regulatory requirements. Empowering employees with knowledge fosters accountability, reducing errors and non-compliance risks. Investing in staff competency strengthens overall operational efficiency and helps maintain high-quality production standards.
C. Proper Storage and Handling of Materials
GMP mandates strict controls over material storage and handling to prevent contamination and deterioration. Raw materials, intermediates, and finished products must be stored in designated areas with controlled environmental conditions. Labels should clearly indicate status, such as "quarantined" or "approved." Proper inventory management ensures traceability and prevents mix-ups. These measures safeguard product integrity and ensure regulatory compliance throughout the supply chain.
VII. Role of Regulatory Authorities
A. Overview of Global GMP Standards (e.g., WHO, FDA)
Regulatory authorities like WHO and FDA set GMP standards to ensure product safety and efficacy. These guidelines form a global benchmark, promoting uniformity across industries and regions. While WHO focuses on international public health, the FDA enforces strict GMP rules in the U.S., particularly for pharmaceuticals and food. Understanding these frameworks helps organizations align operations with global expectations, ensuring compliance and market access.
B. Importance of Regulatory Inspections
Regulatory inspections verify whether companies adhere to GMP standards. These audits assess facility conditions, documentation, and product quality. Inspections identify non-conformities and help organizations rectify issues before they escalate. Passing regulatory inspections builds credibility with stakeholders and consumers, showcasing the company’s commitment to quality and safety. Failure, on the other hand, can result in penalties, recalls, or loss of certification.
C. Penalties for Non-Compliance with GMP
Non-compliance with GMP regulations can lead to severe consequences, including product recalls, financial penalties, and reputational damage. In extreme cases, authorities may suspend production or revoke licenses. Beyond financial losses, non-compliance erodes consumer trust and hinders market opportunities. Adhering to GMP standards is not just a legal obligation but also a critical aspect of sustaining business success.
VIII. Industries Benefiting from GMP Certification
A. Pharmaceutical and Healthcare Sectors
The pharmaceutical and healthcare industries rely on GMP certification to ensure drug safety and efficacy. Strict adherence to GMP guidelines minimizes contamination risks and ensures consistent product quality. For these industries, compliance is not optional but a critical requirement for regulatory approval. GMP certification fosters trust among patients, healthcare providers, and regulators, enhancing the industry’s credibility and global market access.
B. Food and Beverage Industries
GMP is vital in the food and beverage sector to maintain hygiene, prevent contamination, and ensure consumer safety. Adhering to GMP guidelines helps companies meet regulatory requirements and protect their brand reputation. Certification also facilitates export opportunities by meeting international food safety standards. By prioritizing GMP compliance, businesses in this sector build customer trust and achieve long-term success.
C. Cosmetic and Personal Care Product Manufacturers
In the cosmetic and personal care industry, GMP certification ensures product safety and quality, crucial for consumer health and satisfaction. It establishes guidelines for ingredient sourcing, formulation, and packaging. Adhering to GMP helps manufacturers meet regulatory requirements and minimize product recalls. Certification also boosts market competitiveness by demonstrating commitment to high standards, attracting discerning customers and global partners.
IX. Conclusion
A. Summary of the Significance of GMP Certification
GMP certification is a vital tool for ensuring product safety, quality, and compliance across industries. By following its principles, companies minimize risks, maintain regulatory standards, and meet customer expectations. It serves as a benchmark for operational excellence, safeguarding public health and enhancing brand reputation.
B. Encouragement to Pursue GMP for Competitive Advantage
Investing in GMP certification empowers businesses to stay competitive in today’s quality-driven market. It unlocks global opportunities by meeting international standards and fosters consumer trust. Companies embracing GMP gain a strategic edge, showcasing their commitment to excellence and compliance.
C. Final Thoughts on Maintaining Continuous Compliance
Achieving GMP certification is not a one-time milestone but a commitment to ongoing quality improvement. Continuous training, monitoring, and adaptation to regulatory changes are crucial for sustained compliance. By making GMP a core part of their culture, businesses can achieve lasting success and customer satisfaction.
What's Your Reaction?
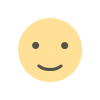
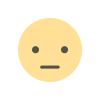
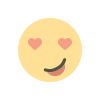
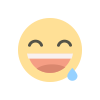
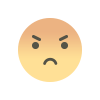
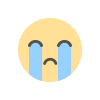
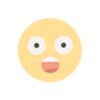